BBQs at the beach, big family dinners, a quick snack on the go – food is a big part of our lives. And each week, millions of New Zealanders head to the supermarket, in store or online, to stock up on groceries.
Foodstuffs, one of the country's two major grocery retailers, sees many of these visits. The company has over 400 retail stores nationwide under the New World, PAK'nSAVE and Four Square brands.
Every year, Foodstuffs' fleet of trucks travels over 34 million kilometres around New Zealand, the equivalent of circumnavigating the globe 850 times! That’s a significant carbon footprint and it's not the only challenge Foodstuffs faces.
"Foodstuffs uses 1 percent of New Zealand's electricity," says Mike Sammons, Head of Sustainability for Foodstuffs, "and the nature of our business means we will always use a lot of electricity. But we can and have made significant improvements when we build new stores or refurbish our existing ones".
"As an organisation our carbon footprint is split roughly three ways, between electricity use, diesel use and refrigerant gas use, with a bit of waste thrown into the mix as well. The challenge for Foodstuffs — as it is for a lot of organisations — is if you want to grow, you need to expand. Every year we build new stores, so our challenge is to reduce our carbon footprint while growing the business."
That’s exactly what Mike Sammons was charged with doing when he was hired as Foodstuffs’ first Head of Sustainability in 2012.
"Almost ten years later and I’m still here," says Sammons. "They can't get rid of me! But in all seriousness, I feel very supported here. It’s good to work with a company like Foodstuffs where you can make a significant difference."
"When I joined, I don't think the company really understood the value of sustainability or energy efficiency. Like many organisations, we adopted sustainable practices if it was cost-effective for the business. But from about 2010 onwards, senior management started to take sustainability more seriously. Since then it has been embedded in most organisations to the point where it's business as usual. That’s definitely the case at Foodstuffs."
Cool your jets
One of the first sustainability initiatives Sammons championed was new refrigeration technology. In 2012, Foodstuffs became the first company in the southern hemisphere to trial CO2-based refrigeration as an alternative to synthetic gases which are a significant contributor to global warming.
"All refrigeration systems leak a little bit," says Sammons, "but synthetic gases are very damaging to the atmosphere. We heard about this new technology in Europe and EECA supported us to test it in New Zealand. We built two new stores in Wellington and we installed the synthetic gas system in one and the new CO2 technology in the other. The results were staggering. Not only was the new technology more energy efficient, it reduced greenhouse gas emissions from refrigeration by 99.7 percent. That project fundamentally changed large scale refrigeration systems not only in Foodstuffs but in New Zealand."
Not only was the new technology more energy efficient, it reduced greenhouse gas emissions from refrigeration by 99.7%.
Since 2014, all new and refurbished Foodstuffs stores use CO2 refrigeration systems and together with a range of other energy efficiency measures, it's led to a 45 percent decrease in the overall carbon footprint for new and refurbished stores. It's not cheap however.
"A new CO2 based refrigeration system costs about $2 million per store," says Sammons, "so we can't change all our refrigeration systems overnight. But we're making significant progress and by 2025 every New World and PAK'nSAVE in the South Island will use CO2 refrigeration systems. The North Island, due to its size, has a little bit of a longer tail."
Put a lid on it
Soon after Sammons joined Foodstuffs, he collaborated with EECA on an energy efficiency study of the stores.
"Before that study, we knew how much power we were using but we didn't know where we were using it," says Sammons. "If you don't know where your energy is going, you can't work out where to invest time and money to reduce your emissions and energy costs. We installed sub meters that provided us with really detailed information about our energy usage at a store level. It told us how much energy was being used in the bakery, butchery, refrigerated goods sections, and our heating and ventilation systems."
All new and refurbished stores now have energy efficiency built in with:
- LED lighting throughout the store
- lids and doors on all freezers and many fridges
- skylights in the roof and/or large windows to provide natural light
- the ability to recapture heat from refrigeration to heat water for use in-store.
As a result, Foodstuffs stores built now (and in the future) have approximately 50 percent lower operational carbon footprint than those built a decade earlier.

Electric dreams
The logistics of transporting New Zealanders’ daily bread and other groceries around the country is massive. Foodstuffs has experimented with electric vehicles, importing 29 electric vans from the UK in 2016 that have collectively done over 1 million kilometres getting groceries to people's doorsteps. Recently they also trialled three electric trucks: a 6-tonne, 11-tonne and 24-tonne truck.
"We've got some great learnings from the project," says Sammons. "The two smaller trucks based in Christchurch haven’t missed a beat since day one, some 18 months ago, and have now clocked up over 60,000kms. The larger 24-tonne truck has been relocated from Wellington to Hawke's Bay, where the flatter terrain should help reliability and performance.
"Are we ready to electrify the entire Foodstuffs fleet? No, because the price is still too high. Electric trucks are effectively three times the cost of diesel trucks and have a much more limited range. When electric trucks do come down in price we will introduce more of them to the fleet, but the cost element is key."
An easier win was a vehicle audit that led to a 30 percent reduction in the organisation's fleet size in the North Island. As well as taking responsibility for reducing their own transport carbon footprint, Foodstuffs is helping customers reduce theirs by installing EV chargers and putting in bike parking facilities at stores.
ChargeNet has installed almost 100 electric vehicle fast chargers in car parks at New World, PAK'nSAVE, and Four Square, which is a significant percentage of the fast chargers in the country. So far, Foodstuffs' customers with EVs have charged and driven 1 million kilometres, saving over 2,300 tonnes of carbon emissions.
In some areas you're relying on new technologies to come to the rescue...But there are lots of easy wins that any company can take advantage of.
Future focused
'What's the next big project?' is a question Mike Sammons gets asked all the time.
"The good news is we've made significant progress as an organisation," he says. "In some areas you're relying on new technologies to come to the rescue, like the natural refrigeration technology for example. But there are lots of easy wins that any company can take advantage of. One thing we are excited about is the potential for solar power."
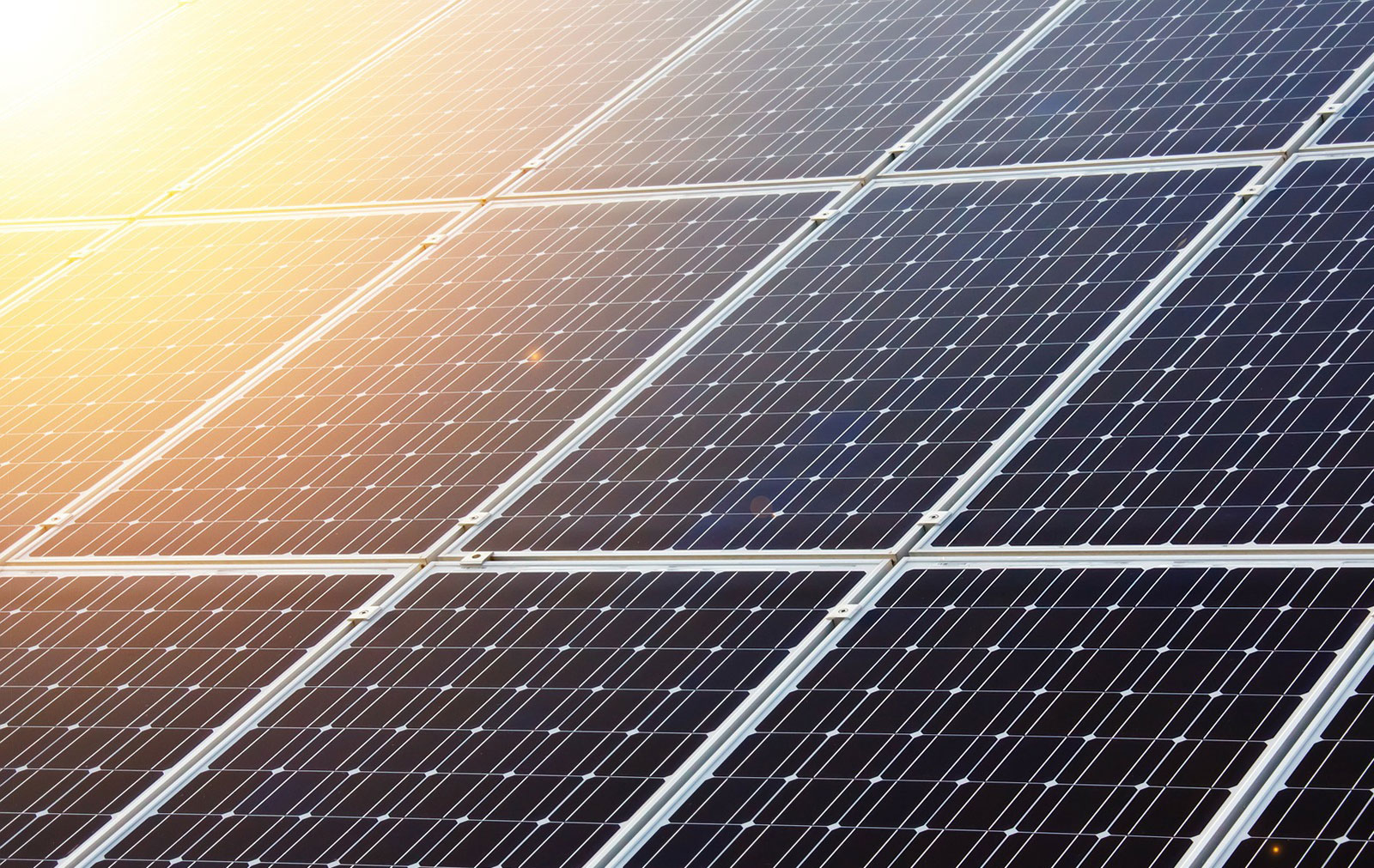
Foodstuffs recently installed the largest rooftop solar array in the country on their new Distribution and Support Centre near Auckland Airport. The solar panels take up the equivalent of 14 netball courts and the office is completely powered by solar.
"It's working brilliantly so far," says Sammons, "and with the cost of solar coming down significantly over the last five years and electricity prices set to rise in the future it makes a lot of sense. Solar power offers us the opportunity to reduce our carbon footprint and keep our emissions tracking in the right directions while reducing the costs for our store owners so it’s a win-win for the environment and the business."